FAQ: Most Common Questions & Answers
A vertical baler is a machine that reduces the overall volume of your loose waste material by making a compact and tight bundle called a bale.
Using the filling opening, you can easily toss your loose cardboard or soft plastic into the baler. A press plate uses extreme force to compress the material by pushing downward. The material remains compacted due to the retainer dogs inside of the chamber of the baler.
Continue to throw material into the baler until you have compacted enough waste for a full bale. Then, the finished bale is manually tied off with polyblend strapping or wire. The size and weight of the finished bale are determined by the size of your baler.
The finished bales take up a limited amount of space and are easy to move. Baling your waste material offers you an easy solution for waste disposal.
Bramidan offers a variety of different baler designs that are perfect for handling your waste.
Our specialists are ready to advise you on the type of baler that will best suit the needs of your business. Please contact a member of our team for further information.
You can compact a surprising number of different types of waste in a vertical baler.
We offer machines to bale:
- Cardboard and paper
- Shrink wrap and plastic packaging
- Plastic PET bottles
- Plastic trays and containers
- Aluminum and tin cans
- Fibrous materials, e.g., cotton and wool
- Drums and barrels
- Expanded plastic (EPS)
- General production waste
- Shredded waste
Contact a member of our sales team to discuss a baler solution for your specific waste type.
The baler model that is best for you depends on the type and volume of material and the amount you generate daily. It also depends on the amount of space you have at your facility.
Using this information, we can determine the proper waste solution for you and your company. Our sales team is happy to work with you to find the best fit for your company’s structure and internal work processes.
Our B series machines all share the classic design with exterior cylinders. These machines were created specifically for baling cardboard, paper, and dry soft plastic (shrink wrap).
Our X series balers are our heavy-duty low-profile machines with interior cross cylinders. These machines were designed to handle various types of bulky waste materials. The X series balers provide a quiet working environment with the lowest noise level on the market.
Our B-series balers are designed to compact cardboard, paper, and dry soft plastic (shrink wrap).
Contact a member of our sales team prior to compacting any other types of materials in your baler.
Our X-series balers are designed to compact a variety of different heavy-duty waste materials, such as plastic bottles (PET), expandable plastic, aluminium or tin cans, and big bags. They are also very efficient at compacting materials like cardboard, paper, and dry soft plastic (shrink wrap).
Contact a member of our sales team before compacting other types of materials in your baler.
Our Flap Door is specially developed for handling PET bottles.
The Flap Door works just like a chute for the bottles and makes it easy to throw bottles directly into the baler either separately or in full sacks.
We offer a door solution that does not swing outwards. To allow more direct access to the chamber from all sides and provide more space around the baler, we have designed a manual vertical door that opens upwards on our B-series machines.
This door option is designed for sites with a narrow, limited amount of space.
Yes, we do. Our 60” baler, the B6030, makes bales that meet standard mill-size dimensions and weight specifications. Finished bales weigh 800 – 1,300 lbs., depending on the material.
The low-profile design allows the baler to fit an 8 foot dock door standing up. Once the cylinders are raised, it can be installed and operated under an 11 foot ceiling.
No, our balers do not have a built-in scale. However, the bale size and weight do not fluctuate by much and will usually be the same.
Our BRA-IN monitoring solution allows you to view the average weight and number of bales made in your baler each week and/or month. You can also create reports for recycling compliance.
Yes, we do offer custom colors as special orders for an additional fee.
The standard yellow color of our balers is based on a scientific study of the basic human psychology that states yellow captures our attention more than any other color. The Bramidan yellow means that our balers are very easy to see in all types of working environments, which reduces the overall risk for accidents.
All of our balers are usually very quiet and can be placed in a variety of work environments without causing a disturbance.
Our B-series vertical balers have a very low noise level that never exceeds 57 – 68 decibels. The noise is comparable to that of a vacuum cleaner or air conditioning system.
Our X-series vertical balers have an even lower noise level that does not exceed 59 decibels. The noise is equivalent to conversational speech.
The weight and size of a finished bale depends on the size of the machine and the waste type.
Our small footprint vertical balers, like the B3 and B4 models, make smaller easy-to-handle bales. Finished bales made in one of these machines weigh between 66 – 220 lbs. for cardboard and 88 – 286 lbs. for plastic. Using a bale cart, the bales can be easily moved around your facility for storage or pickup.
Our medium size balers make a heavier bale that can be ejected and stored on a standard pallet. Finished bales weigh between 440 -772 lbs. for cardboard and 550 – 992 lbs. for plastic. Using a pallet jack or forklift, the bales can be easily transported.
Our large balers, like the B6030 and X30 HD models, make bales that are as heavy as Large Size Balers compact bales as heavy as 825 – 1,200 lbs. for cardboard and 880 – 1,300 lbs. for plastic. View the finished bale size dimensions of our balers under Product Specifications.
Vertical balers are compact, cost-effective, and well-suited for manual workflows and moderate volumes of waste such as cardboard and plastic. They compress material from the top down and take up minimal space, making them easier to place and install—especially in smaller businesses or locations with limited room.
Horizontal balers are designed to handle larger volumes of waste and offer a higher degree of automation. They compress material from the side and can be integrated with conveyors, shredders, and other automated systems. This reduces the need for manual labor and increases operational efficiency. However, they require more space and a higher investment.
The size of the bales depends on the channel baler. Have look at the product specifications here. Bale weights vary depending on channel baler model and material. Expect bale weights between 440 and 660 lbs in the smallest model and 770 and 990 lbs in the largest model.
In general, plastic gives the heaviest bales and cardboard and paper the lightest bales.
We offer a variety of filling options for our horizontal balers depending on your needs, like filling from both sides, from the back, and from the top. Both manual filling and automatic filling is possible.
Please consult with our sales team to learn about the filling options.
The horizontal baler can be placed both indoors and outdoors. The machine requires a solid foundation e.g. concrete or pavement that can support the weight.
If you place the baler outside, we recommend that you place it under a roof to protect it from wear and tear.
Our sales consultant will help you identify the best place to install your baler.
That depends on the compactor. As a rule of thumb, you can use a compactor to compact all soft materials. Examples of soft materials include cardboard, shredded paper, news paper, paper bags, soft dry plastic, and PET bottles.
There are also compactors for wet waste, polystyrene, EPS, and wood.
We always recommend that you consult with us if you wish to use your compactor for any other materials than the listed and recommended materials.
You achieve several advantages by draining your waste. First, wet waste is very heavy. Draining it means that you reduce the weight, density and mass. As a result, you can use smaller compactors and fewer and smaller containers to store your waste in. Ultimately, this means a reduction in the number of waste pick-ups.
Second, wet waste is difficult to process by incineration. Incineration is the process of burning waste to recover energy. Wet waste weakens the burning process and the energy is not released as well if the waste is dry. Therefore, some governments even prohibit wet, moist and undrained waste in incineration facilities.
Yes, you can. The screw efficiently crushes the material into small fragments and ensures that the bulky material does not get stuck or clog the feeder.
This eliminates the need to wait for the press cycle of the press plate — which can take up to a minute — because of the screw’s continuous operation. A screw compactor is ideal for fast clean up, because there is no waiting time.
Yes, we offer special Self-Contained Compactors for organic waste, e.g., waste from foods. Organic waste can leave obnoxious smells or leak through the door.
Our Self-Contained Compactors are specially designed to compact organic, moist, or commercial waste that is similar to household waste.
The press plate in these compactors is self-cleaning to counter smells and the door is sealed to prevent splashing and leaking.
Our static compactors and screw compactors can be seamlessly integrated into already existing waste handling or production facilities and can be connected to inline automation solutions.
Please consult with a member of our team to hear more about your options for automating your waste handling
Yes, you can. However, the type of compactor that you need, depends on the shape and the volume of the wood material.
Please consult with us before using your compactor for wood and other hard and bulky materials.
Our compactors use 3 L / N / PE; 400 V,50 Hz as standard.
The static and Self-Contained Compactor use 16-32 amperes. The screw compactors usually use 63 amperes.
You can check the required power supply for each compactor in the product specific tech specs.
Because it consists of two separate units, the capacity of the container is approx. 50% larger in a static compactor than in a mobile compactor. This makes the static compactor suitable for very large amounts of waste. A static compactor also enables continuous feeding because once a full container is removed for emptying, a replacement container is instantly put in its place. This eliminates waiting time and counters waste heaps.
Another benefit of the static container is that, because it is a static solution, it can be integrated into an existing building or site with hoppers, feeders and solutions for automation.
There are special screw compactors for handling waste that contains a lot of liquids or waste that is very wet.
These compactors combine powerful draining with high compaction. They can be used to separate solid waste material from liquids or to remove residual liquids from waste products. The system effectively drains out free-flowing contents from beverage containers such as plastic cups, Tetra Pak packaging, cans, or PET bottles, or drains sewage sludge and industrial waste.
The drained-out liquid is discharged via a drainage pipe and can be collected in a trough or led further into the drainage system. Drained material is easier to process or recycle and the drained solid waste material can be energetically utilized in incinerator plants. Furthermore, the reduction in weight as a result of draining enables considerable cost savings in waste disposals.
Yes, you can. All our compactors are available in standard RAL-colours. They are painted with a durable lead and chromate free paint.
Furthermore, their large smooth surfaces offer plenty of room for a company logo.
Yes – a screw compactor is designed for handling bulky waste! The powerful screw effortlessly crush even the bulkiest materials. The screw compactor can also handle expandable materials.
By crushing the material before it is compacted, you get a much higher compaction ratio.
In short, the difference between a static compactor and a self-Contained Compactor is whether the press unit stays on-site or if it is attached to and follows the container.
Static compactorA static compactor is designed to stay on-site. The press unit and the container unit are separate units and the press unit is bolted to a concrete base.
The container is attached to the press unit by ratchets. When the container is full, it is picked up for emptying and a replacement container is put into position on the press unit.
The static compactors are very well suited to handle very large amounts of waste and in situations where the is a need for constant filling.
Self-Contained Compactor
In a Self-Contained Compactor, the press unit is integrated with the container. This means that the entire unit is picked up for emptying when it is full.
The Self-Contained Compactor is often slightly smaller and have less capacity than a static compactor, because it must be easy to pick up and transport on a truck.
The Self-Contained Compactor is suitable for applications where space is confined. They can handle a wide range of waste materials including cardboard, paper, plastic, combustible waste or organic waste.
There is no simple answer to this question. Compactors are designed to handle large amounts of waste, but there might be other reasons to choose a compactor solution as well.
When we make an evaluation for you to determine your need for a compactor we consider the size of your company, your internal work structures and processes, waste handling procedures, your work flow, the time you spend handling waste, and your current solution.
All these data help us determine the best solution for you to save time and money on your waste handling.
It depends on the size and the model.
If you want to know the exact weight of a Self-Contained Compactor, please see to the product specific tech specs.
The difference between a static compactor and a Self-Contained Compactors is whether the press unit stays on-site or if it is attached to the container.
A static compactor consists of two separate units – the press unit and the container unit. The press unit is bolted to a concrete base and stays on on-site.
In a Self-Contained Compactors, the press unit is integrated with the container. This means that both the container and the press unit is picked up for emptying.
No, it does’nt. Our compactors are designed for durability.
The machines only require an annual safety check as prescribed by law. During the service check, the service technician will ensure that your equipment lives up to the rules regarding safety and functionality.
We provide a professional service setup designed to meet the needs of our customers, including flexible service contracts. With a service contract from Bramidan, you always have an up-to-date machine with the latest technology and user friendliness.
It is possible to integrate your static or screw compactor with the building, e.g., with a wall hopper that enables feeding from inside directly into the compactor through the wall. This can be an advantage if you generate a lot of your waste inside. With a wall hopper, you can streamline your waste handling by eliminating having to go outside to dispose your waste into the compactor.
Reach out to one of our consultants if you want to hear more about making your waste handling more efficient.
A compactor uses a powerful press plate to compact the waste horizontally into a container.
A screw compactor, which is also sometimes referred to as an auger compactor, combines crushing and compacting. It is extended with a strong rotating screw, or auger. The screw uses powerful rotations to crush and compact the material. The rotating screw pulls the material into the container.
The screw compactor is especially suited to handle bulky materials such as cardboard and wood.
When compared with regular compactors, the waste can be expected to be up to 60% more compacted in a screw compactor.
Before installing your static or screw compactors you need to prepare some structural or site adaptions.
The compactor must be installed on a solid, leveled ground. The press unit must be properly installed by being bolted to the ground, which must be concrete or pavement, or by being bolted to the building.
You also need to lay out guiding rails in the floor to make sure the container unit is positioned correctly on the press unit. Finally, you need to make sure that you have the correct electrical connection in place.
Our experienced team of consultants can help you clarify what you need to take into account and what you need to prepare to get the best start with your compactor.
A compactor is very safe to operate and requires no special skills. All compactors are reliable and thoroughly tested to ensure that they meet the highest safety standards.
Everyone can safely load the machine. All mechanical and electrical parts are placed inside the machine, out of reach for users. Furthermore, several safety features are in place to protect the user. The control panel is placed on the outside of the machine and gives the user easy access to start the machine. An emergency stop is also placed on the control panel within fast and easy reach.
Our compactors are manufactured by our trusted German collaborator, Presto. Presto has more than 50 years of experience within the area of environmental engineering and their products are highly recognized in the business. They all carry the EU CE marking and meet the essential requirements for health and safety set forth by the European Union. In addition, two machine groups are certified according to GS, Geprûfte Sicherheit, which means that they have been tested by a German state-approved independent laboratory to prove and ensure their safety.
As a company, Presto is certified with the ISO 9001 and SmS, Sicherheit mit System, certificates, which means that the company assesses and considers the quality and safety requirements of their customers and the requirements of the applicable standard. This is your guarantee that each Presto product will meet or beat the highest requirements of safety anytime.
Wet waste is difficult to burn for two reasons: steam and cooling.
When water boils, it creates steam. The steam displaces the oxygen around the flame. With less oxygen available for burning, the flame will slowly suffocate. Cooling relates to the temperature in the burning pile. Water boils and vaporizes at 100˚ Celsius. Most materials need much higher temperatures to burn. Since water has the lowest burning temperature, the temperature will not rise to more than 100˚ Celsius until all the water has vaporized from the pile. This means that the other materials will not burn properly if there is water in the pile. As a result, the combustion process will never be properly utilized if the waste is wet.
Yes. We offer very flexible rental agreements and both short-term and long-term rentals are available.
After the rental period, you can extend the rental period, buy the machine, or give it back to us. To get the most out of your compactor and to keep total track of your expenses, you can add a service agreement to your tenancy. The service agreement can be an annual service check or a full-service agreement throughout the entire rental period.
Contact one of our sales consultants to hear more about the flexible possibilities about renting a compactor.
A waste compactor, is, as the name suggests, a machine that compacts waste. They are large and heavy-duty machines that can take mixed waste in large quantities – several tons at a time – and compress them into a smaller and more contained amounts.
The compactor consists of a press unit and a container unit. The press unit compacts the waste horizontally into the container. When the compactor is full, it is picked up by a waste collector. Depending on the material, it is then transported to a recycling station or an incineration facility. Compactors are available in a range of sizes and varieties depending on the type of material and the amount and volume of waste the machine will be processing.
Yes, you can. If your compactor will be placed in a place with public access, you can prevent unauthorized people from using it with a digital auto lock.
The lock prevents people from throwing waste into the compactor and running a press cycle. The lock can be controlled with a pin code or a key tag. This way, only you and the people you give the pin code or a key tag to can use the compactor.
A digital auto lock can be a good idea if many people have access to the compactor, if the compactor is unattended, or if people have access to the compactor during all hours of the day.
There are several advantages of draining your waste.
Cost savings and revenue
You can significantly reduce your costs for waste disposal if you drain your waste.
Damp and wet waste is very heavy. Draining out liquids reduces the weight and the density of your waste. Your waste takes up less space – and as a result, you can use smaller compactors and fewer and smaller containers to store your waste in. You can also reduce the number of waste pick-ups significantly, because you can store a lot more waste on-site.
The result is an instantly positive effect on your waste handling bill.
The drained-out liquids can also be collected and sold to producers of biomass and converted into biofuel. Biofuel is fuel that is developed from organic materials, a renewable and sustainable source of energy used to create electricity or other forms of power.
Selling your residual liquid as biomass can help you generate a profit from your waste. This increases the write-off of your equipment.
Incineration
Drained material is easier to process by incineration. Incineration is the process of burning waste to recover energy. Energy from incineration is used for electricity and district heating. However, wet waste weakens the burning process and the energy is not released as well if the waste is dry.
With a screw compactor, you get up to 90 pct. reduction in volume of your polystyrene and expandable plastic.
Polystyrene and other expandable plastic materials contain roughly 98 pct. air. The screw compactor divides the polystyrene into fine granulates and turn them into blocks that are easy to stack on a pallet.
The process of forming blocks is like this: The granulates enter the baler channel via an auger. Here the counter pressure causes friction and thereby heat. The friction heat make the granulates melt slightly. This removes the air and reduces their size. The melted granulates stick together and can be compressed into high density, manageable blocks.
Many people are not aware that polystyrene is recyclable. But it actually is very easy to recycle.
High density compressed polystyrene is easy to process into new plastic or foam products. Polystyrene is reused in almost every plastic product imaginable, from mobile phones, speakers, TVs, and toys. Reusing polystyrene is much cheaper – and more environmentally friendly – than producing new plastic.
This means that polystyrene is a very sought-after commodity that is very popular in e.g. China where a lot of plastic is needed for production.
It depends on the quantity and the type of polystyrene.
Our machines are built very sturdy with reinforced and rust resistant elements to enhance machine life time.
An EPS granulator divides the polystyrene into fine granulates. This reduces the volume of the polystyrene by a third.
The granulator is fitted with a bag inside the machine that collects the granulates. The bag is easy to dispose of in your container.
Polystyrene is an inactive material that doesn’t decay. When polystyrene is sent to a landfill it will stay there forever. Therefore, it is important that you handle your polystyrene responsibly.
If you handle a lot of polystyrene, compaction and recycling will reduce your total waste handling costs. When you compact your polystyrene, it takes up less space in your container. You can save money on waste collections and container rentals – and you take responsibility for the environment.
As a rule of thumb, you can granulate all types of polystyrene that you can break with your hands.
For polystyrene products that are more heavily compressed, e.g., insulating plates containing fire-retardant additives, XPS, or damp EPS, you must use a screw compactor.
Yes, most of our balers can easily handle 60” widescreen TV boxes.
Our widest machines, the B6030 and X6030 balers, can handle up to 65” widescreen TV boxes. There is no need to break down the boxes first. View the filling opening dimensions on our balers under Product Specifications.
The most imporant thing is to make sure the cans are empty prior to baling them. You do not need to clean them.
We offer a drain system add-on with a drip tray to catch liquid residue on select models .
Yes, cardboard boxes can be recycled very easily and efficiently. By recycling cardboard, you are reducing your environmental footprint while also contributing to the reuse and production of new cardboard material.
Cardboard is recyclable as long as it is dry and not contaminated with food or oil. Cardboard can be recycled many times over. The majority of cardboard is composed of about 70 – 90% recycled materials; however, some is composed of nearly 100% recycled materials.
During the recycling process at the paper mill, cardboard is first shredded into tiny pieces, also known as fibers. Next, the fibers are mixed with water and chemicals to be broken down. The end result is called pulp.
The pulp is then filtered to remove any and all debris, such as tape, glue, metal, dyes and ink. After it has been thoroughly cleaned, the pulp is left to dry. Once the drying process is complete, the pulp is then formed into solid sheets, or linerboards, which are glued together in layers to create new cardboard.
Yes, we supply a drum crusher that is built to do just that. Our drum press is designed to crush standard 55 gallon drums and other non-explosive drums.
The press plate contains spikes which puncture the drum and remove air for a compaction ratio of up to 90 pct.
You can easily throw whole shoe and boot boxes into any of our small footprint balers. These balers is designed to take up a minimal amount of space.
View the filling opening dimensions on our balers under Product Specifications.
Yes, we supply a draining add-on for select models. With this solution, you will be able to bale waste materials that contain liquids, such as aluminum cans and PET bottles.
To prevent splashing, our draining system also includes a seal for the bottom door.
Yes, you can bale cans and other light metal waste (ie. aluminum) in a baler.
To bale cans, you will need a machine with a high press force that will compact the material during the first press cycle. With cross cylinders and long cylinder strokes, our X-series balers are designed for compacting cans and other heavy duty materials.
For a tight and stable bale, we suggest layering a piece of cardboard on both the top and bottom of the finished bale. Another option is to cover the finished bale in shrink wrap.
Soft plastic can be compacted in all of our vertical balers. The volume and shape of your material will help to determine the machine that is right for you.
A variety of products contain soft plastic recylable material. The most common types are plastic wrappers, stretch film and shrink wrap for goods delivered on pallets, soft carrier bags, and bin liners.
The better sorted the material, the higher the purity; and possibly the value as well.
Yes, our X-series balers are perfect for compacting aluminum waste. These models are designed with X-shaped internal cylinders that create a very high press force. As a result, you are left with a very tight bale that is compacted during the first press cycle.
We recommend our X30 HD and X50 HD balers if you are planning on baling aluminum waste. To keep the bale stable, we suggest laying a piece of cardboard on both the top and bottom prior to compacting. Another option is to cover the finished bale with shrink wrap.
Yes, you can easily use the same machine for both waste types, but not at the same time. We suggest making separate bales of solely cardboard or plastic.
While you are baling cardboard, collect and sort soft plastic waste, like shrink wrap. Once you tied off and ejected the cardboard bale, begin to make the plastic bale.
Yes, it is possible to bale PET bottles. However, before compacting, the bottles need to be perforated or the lids taken completely off. If not, the trapped air inside of the bottles will cause a looser, less compact bale. PET is one of the most abundant materials. It is found in soda bottles, water bottles, drinking cups, and food containers.
PET bottles can be baled in our X-series model balers. For a tighter and more stable bale, we recommend placing a layer of cardboard on both the top and bottom of the finished bale.
Yes, our medium sized balers are perfect for cardboard fruit and vegetable boxes. These machines can handle a wide range of sizes, including cardboard grocery crates, cosmetic boxes, and stacking fruit and vegetable containers.
View the filling opening dimensions on our balers under Product Specifications.
Our balers are high-quality machines that are designed for a minimum amount of maintenance and low costs.
Depending on the type of baler and level of use, we recommend preventive maintenance once a year to keep the equipment running long term.
When the baler is full, the orange full-bale indicator light located under the start button will blink. The press plate will also stay in the down position. This prevents the chamber from being overfilled.
We also offer our BRA-IN monitoring solution, which automatically updates you when your machine is full. You will receive a text or email when the bale is finished, telling you it is time to tie off and eject. Our monitoring solution also allows you to notify your recycler or hauler when an agreed upon number of bales are ready for pickup. Learn more about BRA-IN Bramidan Intelligent Monitoring Solution.
All of our small footprint balers have a single-phase power pack for easy installation.
Our low-profile X10 HD baler is available with both a three-phase or single-phase power pack.
Yes, we do.
Contact a member of our sales team to hear about the different power packs we supply.
Yes, Bramidan balers are safe to operate. Our vertical balers meet the highest safety standards. All of our equipment is accredited by ANSI Z245.5 and OSHA Safety Standards. All control panels are UL and CUL approved.
To protect users, all moving parts are placed inside the machine. In order to eject a finished bale, the operator must stand safely next to the machine and use a two-handed ejection system.
All of our balers have a special pre-load system, which makes it both safe and easy to tie off a carboard or plastic bale. Since the wire and strapping is loaded prior to baling, there is no need to go behind the baler.
- While the baler is empty, pull the strapping or wire along the channels inside the chamber and secure with a loop at the front of the machine.
- Baler is ready to use – toss in material and make a cardboard or plastic bale.
- When baler is full, pull the strapping or wire from the back of the chamber to the front. Tie with the loops you made earlier.
- The machine has a knife attached to easily cut strapping.
- Eject the finished bale.
Depending on the dimensions and max load of your elevator, this may be possible.
Please consider extra space around the machine for packaging and wrapping, if you plan to transport in an elevator. Our balers are not delivered on pallets, as they are always manufactured with lifting groves. All of our balers are shipped standing up. In the case of transporting balers from our B-series, it is possible to lower the external cylinders to keep the height as low as possible. However, this requires extra service hours and may incur an additional fee.
No, our machines are very easy and simple to operate.
To start the automatic press cycle, press a single button and walk away. When the bale is finished, use the turnbuckle to open the lower door. Tying off the bale is very easy with our unique pre-loading system.
Yes, we can modify the machine’s power pack to match most power requirements.
Contact a member of our sales team to find a solution that is right for you.
The best place to install your baler depends on your internal work procedure and waste flow. We suggest placing the baler near the waste source to allow for more efficient waste handling.
We are happy to help you find the best location for your machine.
We recommend placing the machine indoors. If it is outdoors, it must be placed under a covered roof in weather that is not excessively cold or rainy.
Be aware that placing the baler in a consistently cold environment will affect its performance. If it is located in an area that is very cold, we recommend a special hydrualic oil to prevent potential issues.
Contact a member of our sales team if you are interested in placing a machine outside or in a cold environment.
Check that hoses are connected properly.
Other possible issues: Possible limit switch/sensor issue, call for service. Possible pressure switch issue, call for service. Possible directional valve issue, call for service.
By compacting your recyclable waste, like cardboard and soft plastic, in a vertical baler, you can significantly reduce waste handling costs at your facility.
You will also reduce the overall volume of waste, removing the need to rent containers and allowing for less pickups. You save space in your facility, improve internal logistics and create a more efficient work flow.
Contact us today to discuss how we can help you find a baler solution that’s right for you.
The type of waste handling equipment you need depends on a number of different factors: The amount of waste you generate on a daily basis, as well as the waste type. Another factor to consider is the amount of space you have in your facility.
The right waste solution should be tailored to your company’s structure and internal work processes to ensure a perfect fit.
A member of our sales team can assist you in making the right decision.
Bramidan has been in business for nearly 50 years, with more than 1100,000 machines installed worldwide.
We are one of the largest suppliers of vertical balers and compactors in the industry with distributors located in almost all 50 states.
Our equipment prices are very competitive and the Total Cost of Ownership (TCO) is low.
Please contact a member of our sale team to compare the total costs of your current waste management solution. Through this analysis, you will be able to determine the total savings and yield of investing in a Bramidan baler.
Yes. We offer a free trial which allows you to try out the machine in your facility.
If you decide not to keep the machine at the end of the trial period, the only expense you are responsible for is return freight to one of our warehouses.
Yes, we offer used, refurbished, and demo machines. Our pre-owned inventory varies depending on the current stock.
Please contact a member of our sales team for available pre-owned balers.
All of our balers are equipped with BRA-IN technology. BRA-IN is a web portal for intelligent fleet monitoring. Using a modem, machine data is collected.
With BRA-IN you can:
- Control your entire fleet of machines
- Receive a text message or email when there is a full bale
- Advise your recycler directly when a bale is ready for pickup
- Track the number of bales made over time
- Save time and money with remote service and troubleshooting
- Calculate the total cost of ownership
Depending on your specific needs, fully automatic waste solutions are available.
Please contact a member of our sales team to learn more about our automatic solutions.
Yes, we offer customized versions of our vertical balers in a range of different colors.
Please contact a member of our sales team for more information.
Different waste can be baled, such as plastic, paper, cardboard, PET, foam, or other recyclables.
Questions? Contact Us Today
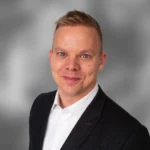
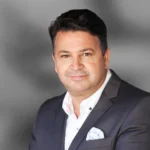
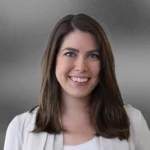
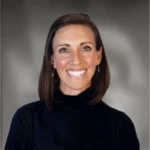