Save Money and Reduce Your CO2e, with BRA-IN
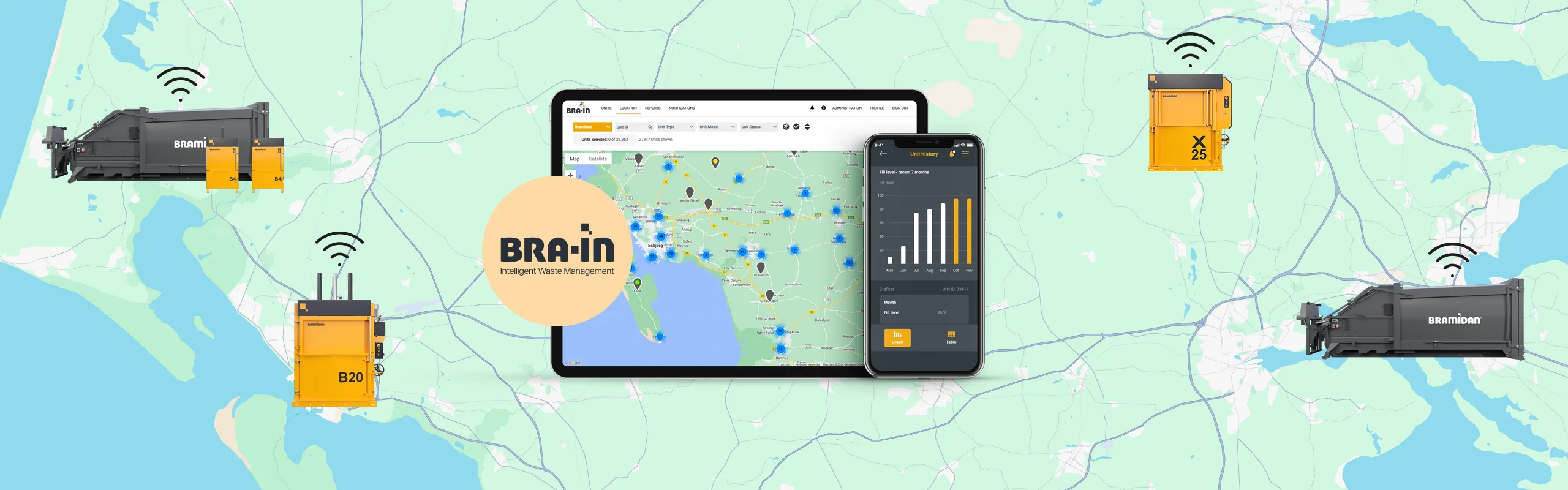
Transform Waste into Value with BRA-IN
Why BRA-IN:
- Connect, Monitor, and Analyze: A full overview of machine performance and remote service support
- Enhanced Waste Collection: BRA-IN Optimize lowers your transportation costs and CO2e
- Automated Notifications: Receive up-to-date reports and request waste pickups.
- Detailed Insights: Equipment status, service needs, and more.
Whether you have a single baler or a fleet of recycling equipment, explore our multiple BRA-IN plans below.
BRA-IN for Balers and Compactors
Not sure which plan is right for you? Learn more about BRA-IN Connect and BRA-IN Optimize below, or contact us.
BRA-IN Connect
BRA-IN Connect works with all new balers and compactors from Bramidan. With easy access to our BRA-IN portal, you can monitor and manage your equipment digitally.
- Remote Service Support: Proactive maintenance, remotely checking and adjusting machine settings.
- Automated Notifications: Get real-time alerts about your equipment’s status.
- Machine Linking: Connect multiple balers into one system for optimized waste pickups. BRA-IN notifies you when a preset total is reached.
- Track Equipment Location: Know where your balers and compactors are at all times.
- Access Performance Data: View detailed production data, like the number of bales produced.
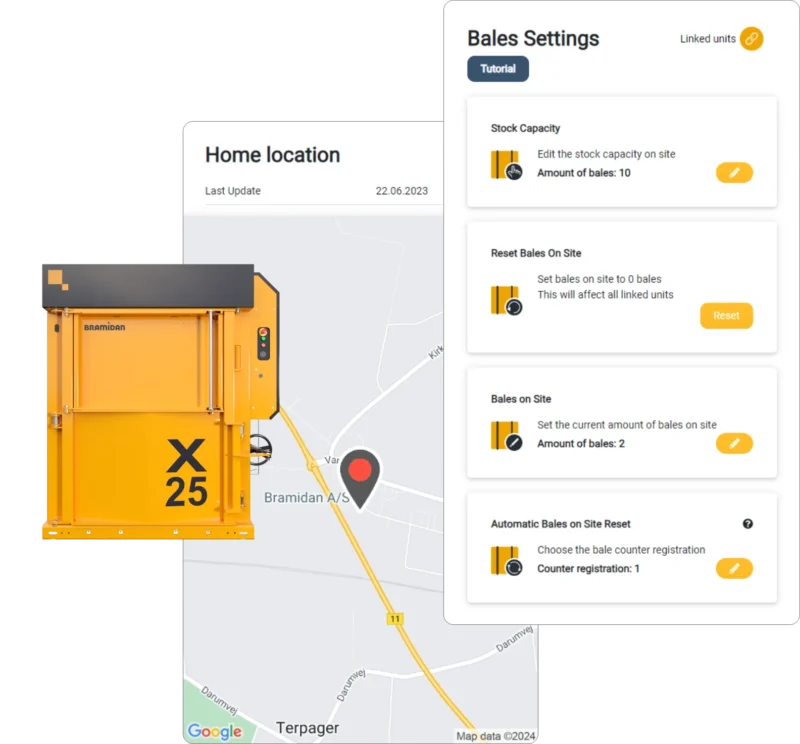
With BRA-IN you can link endless number off on-site balers together to optimize your waste pick ups.
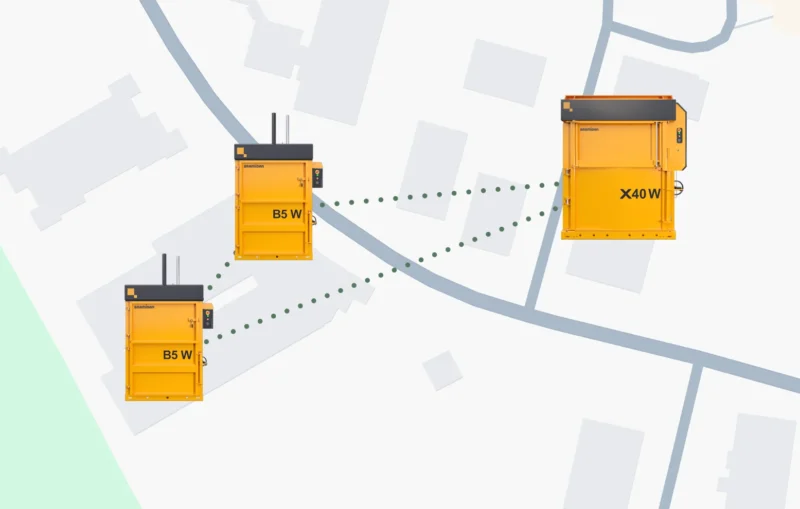
BRA-IN Optimize
With BRA-IN Optimize, your waste management schedule is automatically communicated to your local waste handler. Meanwhile, our BRA-IN specialists continuously audits your strategy for potential savings while lowering your CO2 footprint.
BRA-IN Optimize reduces the number of pickups by up to 25% per unit by optimizing the fill level of up to 80% before emptying, lowering your transportation costs and related CO2 emissions.
- Monitor and Optimize: Our BRA-IN team continually improves your waste collections, ensuring that machines are emptied only when they are over 80% or when strategically appropriate, such as before weekends.
- Fleet Management Performance: Track machine performance data and easily connect to investigate and adjust settings if the machine is not performing as expected.
- Remote Service Support: Proactive maintenance, remotely checking and adjusting machine settings.
- Automated Notifications: Get real-time alerts about your equipment’s status.
- Track Equipment Location: Know where your compactors are at all times.
- Access Performance Data: View detailed production data.
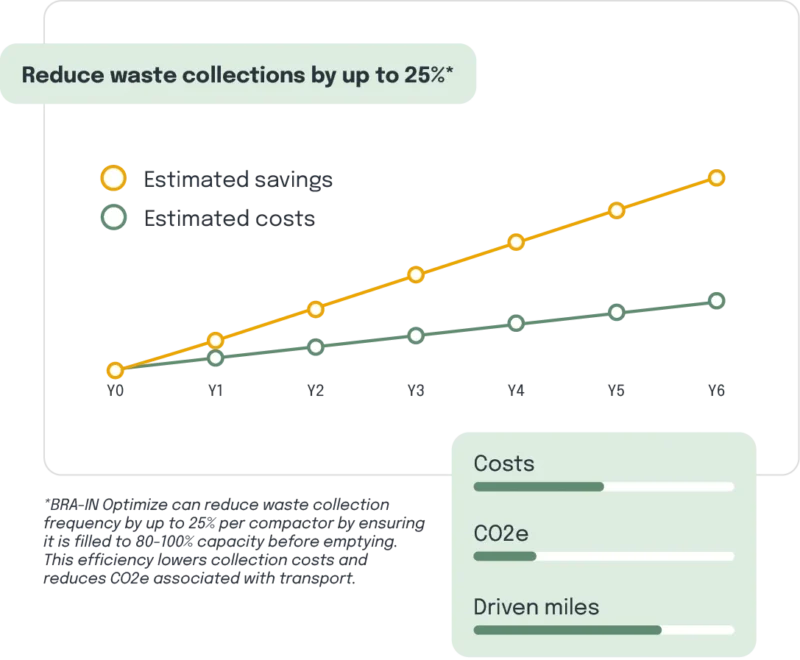
Our BRA-IN specialists continuosly audits your strategy for potential savings while lowering your CO2 footprint.
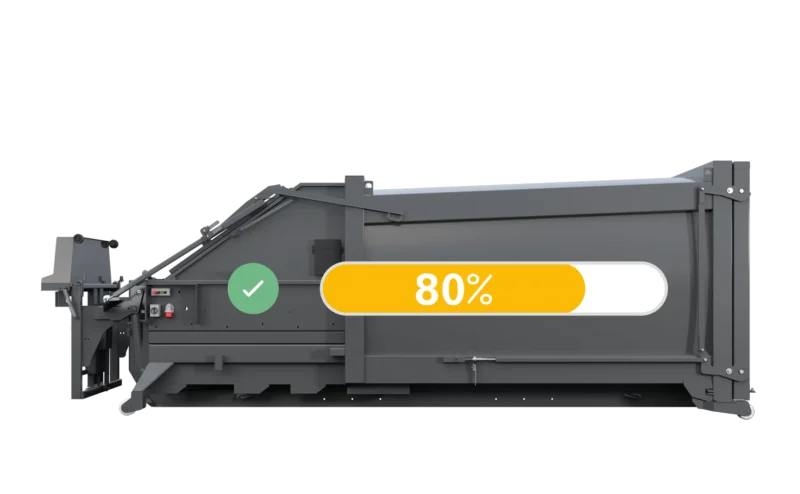
We chose to fully implement BRA-IN Optimize because of the many positive results we saw during our pilot project. We were able to immediately lower our costs by maximizing fill levels, and there was a noticeable drop in CO2 emissions as well. We see a perfect alignment between the effects of Optimize and Salling Group’s strategy to make a difference in the society we’re part of.
— Kasper Bech Guldmann, Senior Category Buyer, Salling Group
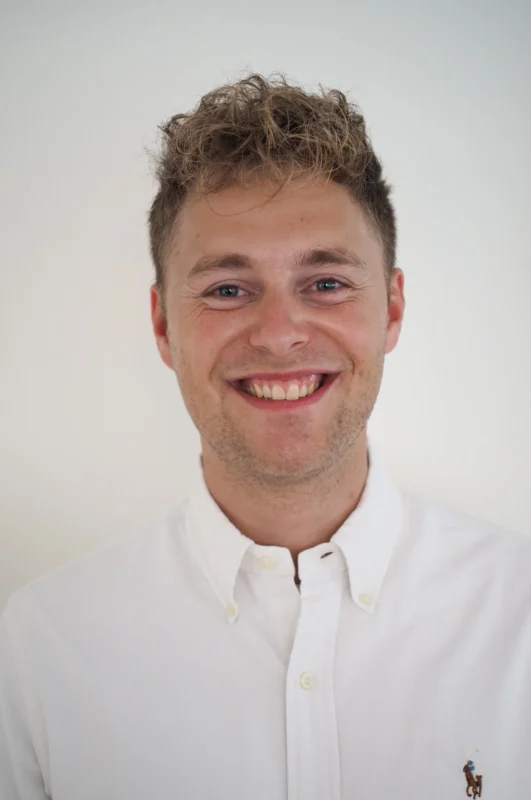
Watch BRA-IN Optimize in Action
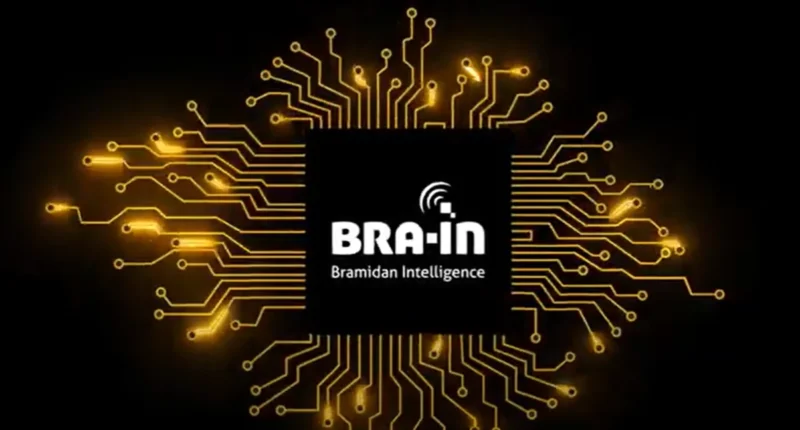
360-Degree Overview of Your Recycling Equipment Fleet
Monitor your entire fleet with the BRA-IN web portal and app. Our accessible digital platforms help you make faster and better decisions, reduce operational costs, and minimize your impact on the environment.
- Remote Service Support: Easy troubleshooting, extended machine lifespan, reduced repair costs and optimized operations.
- Data Collection: Track fill levels, bales ready for collection, equipment errors, and more.
- Machine Linking: Connect multiple balers into one system for optimized waste pickups. BRA-IN notifies you when a preset total is reached.
- Visualization: Monitor performance and location of your machines in real-time.
- Interaction: Receive notifications for timely responses to issues, improving efficiency and reliability.
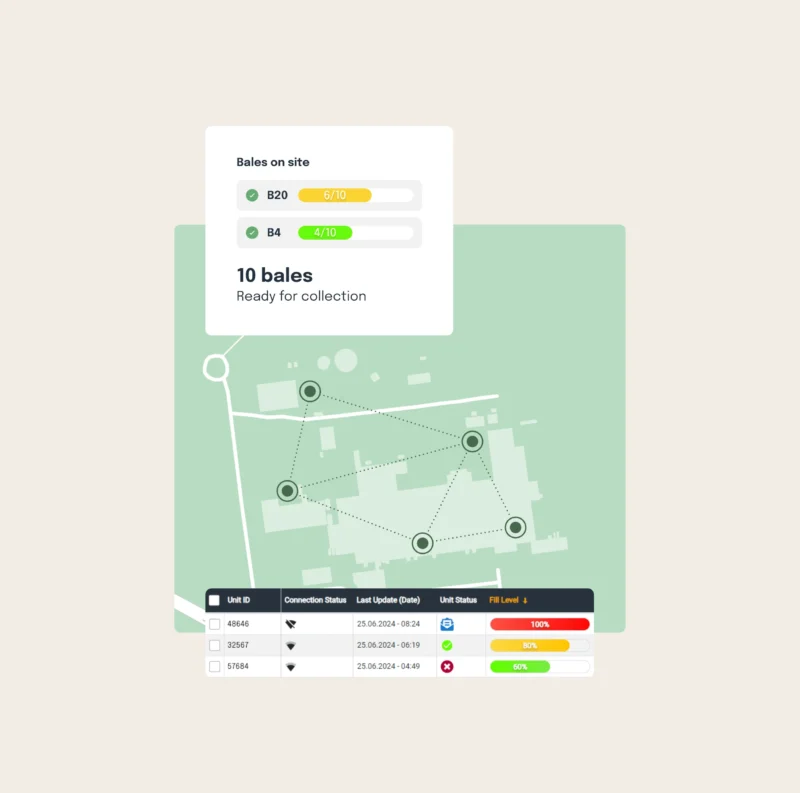
Extra BRA-IN Options
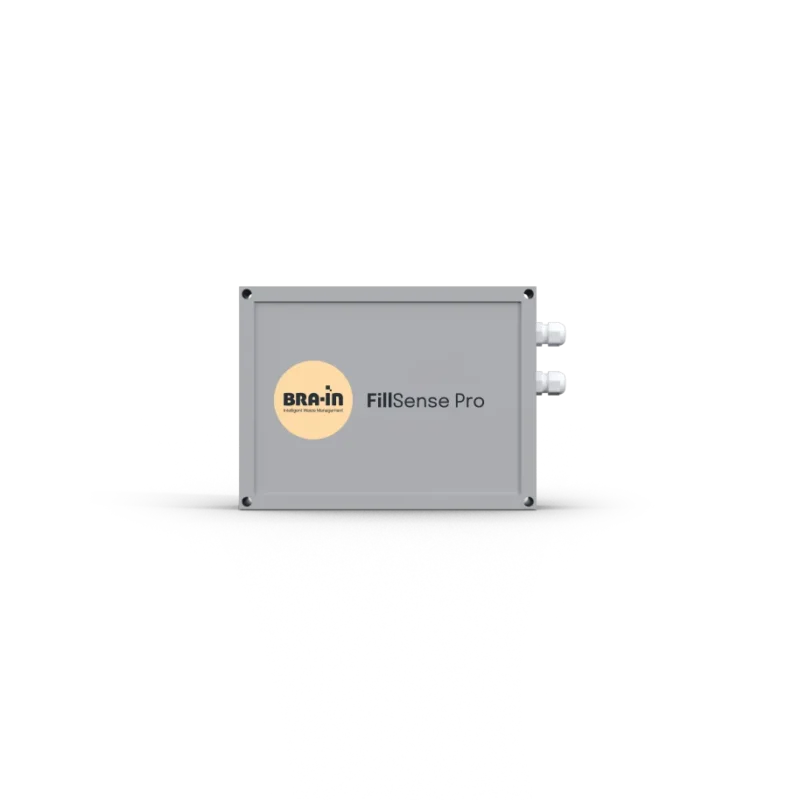
FillSense Pro
With BRA-IN FillSense Pro you can control fill levels on 3rd party compactors. Learn from the data to optimize your fill levels, and reduce your cost on transport.
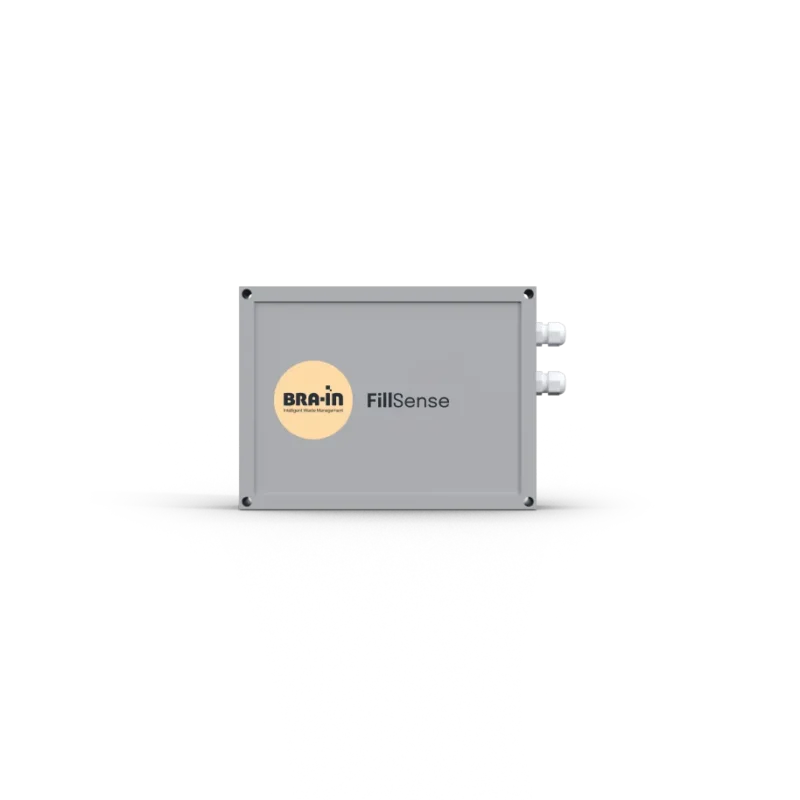
Fill sense
Install the sensor to receive notifications when your machine is 80-100% full. Easily connect to the BRA-IN portal to monitor operational status and access reports on usage and fill levels.
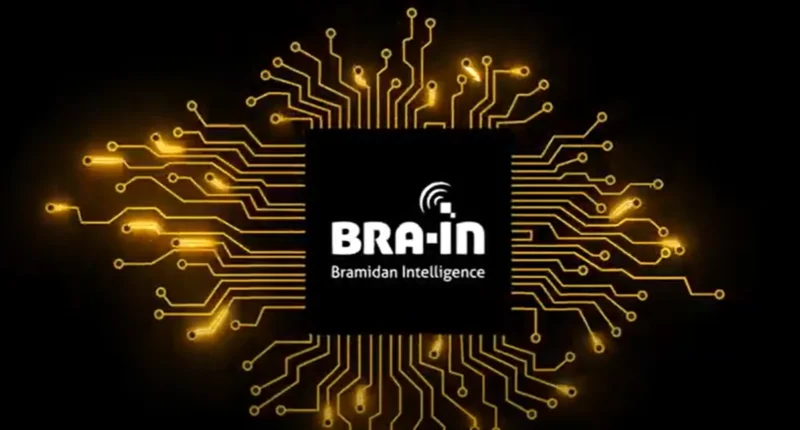
API
BRA-IN allows you to automatically export data via API, enabling you to monitor machine data and information within your own system whenever and wherever you need it.
We strive to make a difference in the recycling value chain, enabling sustainable growth for our customers. Our commitment goes beyond providing convenience and saving; it’s about investing in the future of sustainable waste management.
With upcoming regulations such as the Corporate Sustainability Reporting Directive (CSRD) and the global agenda to reduce CO2e emissions, the demand for recycled waste materials is increasing.
This shift underscores that compaction is a strategic investment in the future of sustainable waste managment.
Our dedication to sustainability and innovative solutions empowers our customers to meet these new demands, ensuring a more efficient and sustainable value chain.
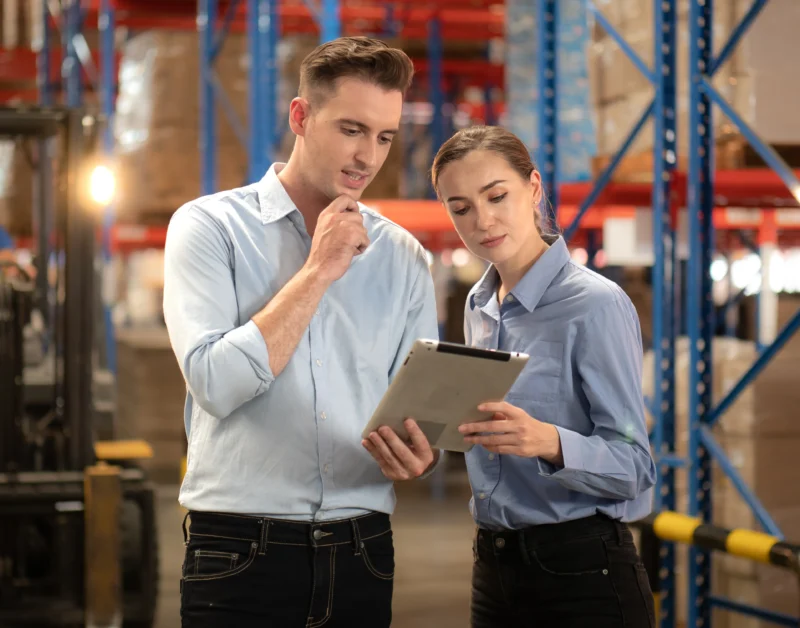
Easy Access via Desktop and App
With BRA-IN it is easy to manage your waste and recycling activities in one easy-to-use platform which ca be accessed by either web or app.
Perfomance data is easily accessible either by deskop or mobile app, presented in clear and intuitive dashboards. This insight empowers businesses to make informed decisions, optimize operations, and maximize the efficiency of their waste management.

Webportal
Status of machine: Design the Portal with information of your relevance such as unit status, site user, motor running hours, days of installation, and much more.
Location of machine: Get full control of where your machines are located. Map pointers give you an overview of your entire fleet, by address or GPS location.Output data: Create reports to show production data from your equipment. Learn how your machine is really used.
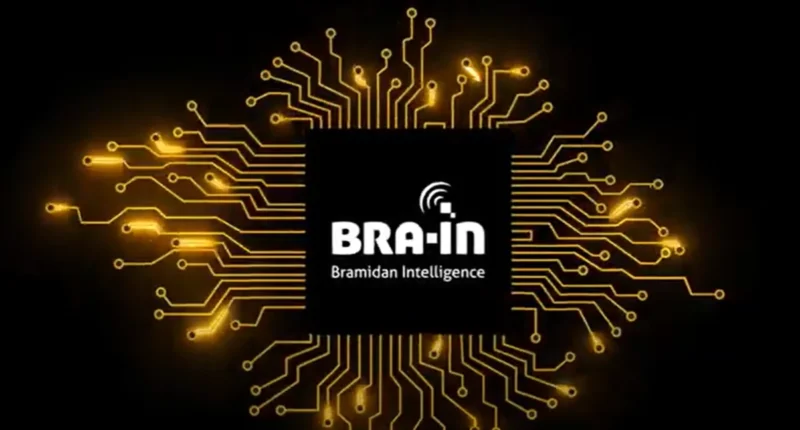
BRA-IN App
Notifications: Get full control of the performance of your machine through notifications, directly on your mobile. You can get notifications about finished bales, machine errors, bales ready for collection and more.
Pick up finished bales: Your can order pickup of finished bales to your waste collector – directly from the App. You can even let your machine send an automatic notification to your waste collector.
How to operate: From the App you have direct access to videos about how to operate your machine, instruction- and spare part manuals, and electrical diagrams.
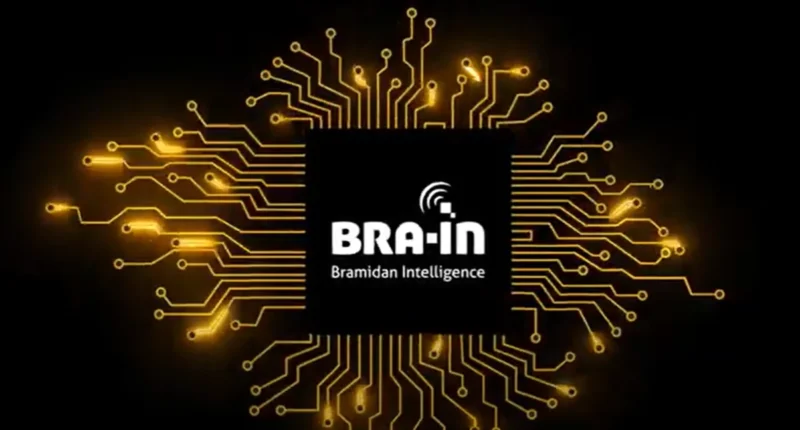
Most Common Questions & Answers
Questions? Get in touch today
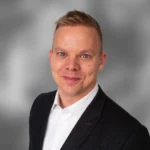
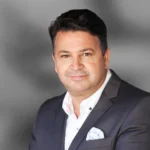
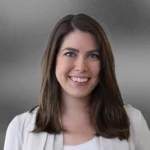
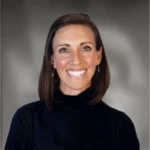